
The finished piece!
A special thanks goes out to Mike McDermott (BillyBob884 on DeviantArt) for his pepakura skills: he put together a pep file of the Combat Shotgun available in very handy PDF format, that I referenced more than a few times during the course of this project. Thanks dude!
I should mention, this is a MASSIVE write up. Grab a cup of coffee, you're gonna be here a while.
This project is, I suppose, a bit more technical than some of the others I've done in the past. I think one of the nice part about my write ups is that things are largely pretty approachable. Recently I've made a really large vacuum forming machine, gained access to a laser cutter, and for this specific project I channeled my old Furniture Design degree and picked up a miniature milling machine to work with aluminum. While many of my previous projects require something akin to a bandsaw as the most complex tool, this shotgun is definitely not a "beginner" project.
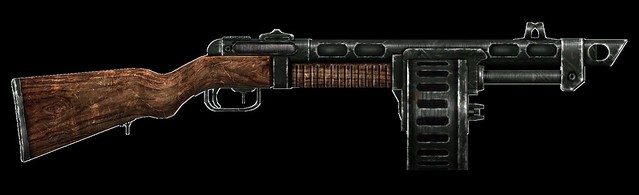
Game render of the Combat Shotgun
Even still, the roots are similar. I started off by making blueprints in Illustrator, based on as much in-game reference as I could pull together.

The combat Shotgun is based quite heavily on a Russian machine gun put into service during WWII, the PPSH-41. Barrel heat sink, sights, drum magazine - many parallels can be drawn between the two designs. I started off with a PPSH diagram lifted from a vintage WWII manual which gave accurate millimeter dimensions of all the associated parts. I scaled the stock on the Combat shotgun to that of the PPSH rifle, and the remainder of the blueprint was scaled accordingly.

I chose to make the stock on the gun from laminated sections of red oak. The areas for the trigger mechanism and barrel mount were cut from the center section before gluing the sheets together, as this made these recessed cavities much easier to construct as opposed to chiseling them from a solid chunk of wood.


Red oak is about as easy to sand as a block of concrete, so more drastic methods were used to get the stock into shape. I started out with a rather angry looking grinding drum and gradually worked my way through 50 grit sanding paper all the way up to 400. I attempted to chisel out some sections, but the oak splinters very badly and I found grinding to be the best method of getting the proper look and feel.


The forward grip was also shaped from a block of red oak. The grip channels were added on my mill with a (very long) bit. It's what I had! The lower grip sits on a long threaded rod which passes into the rear stock and the magazine catch.



At this point I switched over to the drum magazines. These parts are assembled from three pieces which are all vacuum formed from ABS plastic. The bucks were made from MDF with acrylic parts and furniture tacks used for added raised details.



After the ABS was pulled over the bucks and trimmed out, the center section was inserted into a PVC coupler and gently heated until it retained the proper curve to match up to the front and back plates.

This is one of the magazines loosely assembled to check for fit.

These still needed a fair bit of additions to be functional. The finished gun was supposed to be able to exchange magazines easily, and I'd decided on a magnetic catch to hold them in place. Also, while the ABS held its shape fairly well, the large flat sections flexed very easily. The shot below shows the interior bracing of one of the ammo drums. The clear acrylic makes sure the outer panels don't flex inward, while the white styrene ring keeps the side panel in place during gluing, ensuring a proper tight fit.

The upper sections of the magazines were cut out in a semicircle, and an ABS pipe was glued in place (sanded down from the last shot below, that was just rough placement.) The inner diameter of this pipe matches the outer diameter of the heat shield on the gun, where matching magnets were mounted. A large ceramic magnet was epoxied to the inside of this piece before gluing the magazine shut.



The last pieces for the drum magazine were the alignment panel and wing nut. The white piece on the front here mates up with a channel in the magazine holder on the gun, which makes sure the magazine doesn't shift around The wing nut is a piece I molded in order to make multiple copies for multiple magazines.

Getting back to the meat of the build, I had sourced a few different diameters and thicknesses of aluminum pipe for the barrel and heat shield. Over the course of the project, I milled/drilled/tapped dozens of holes in these pieces for various elements.



This area of the gun is the inside of the magazine holder, and the four large holes mark where 4 neodymium magnets are mounted to hold the magazine in place. The slot cut out of the inner barrel makes sure this clears the magnets when all the parts are installed. The magnets themselves aren't actually glued into anything; they sit inside the drilled holes and pull towards a steel plate held in place on the inside of the heat shield. The pull on these is much stronger than the pull against the actual drum magazine, so they're not going anywhere.


The magazine holder itself was made out of several pieces of laser cut acrylic, laminated together. Might be hard to follow the progression from the first shot to the second here, but these are just a bunch of flat parts glued into a big brick!


A few additional elements were made out of lathed urethane resin for the mag holder. These make up the small round drums in the front and back. The front piece had to be sanded to shape to mate up with the heat shield, so I spray mounted some 120 grit paper to a section of scrap pipe and gradually removed material until I had the desired shape.


This U-shaped channel in the front mates up to the panel on the front of the magazines mentioned earlier. The rounded edge makes it easier to get the magazine into the slot even if your approach is a bit off.

There's a large block on the front, which probably has a name I can't identify, which was made with a similar "layered" process. The base parts were all trimmed in 1/8" acrylic, and the various sized holes correspond to screws and pipe that need to fit into the front and rear sections of the part.

This pic explains that last sentence a bit better. The rear of this block holds the grip piston in place, while the sling swivel is mounted to the front.

In the shot above you can see the finished forward sight and ghost ring. These both started life as boring chunks of aluminum. The ghost ring was gradually hammered over a round buck (for much longer than I'd expected) to get the proper shape. Holes were drilled in the mounting tabs that lined up to tapped holes on the heat shield.


The actual forward sight was a block of 1/4" thick aluminum milled down into something a little narrower and more detailed. I am very lucky to have inherited some of my grandfather's milling bits which have enabled me to do small detail work like this without having to sell a kidney in order to afford the necessary mill accessories.


Speaking of aluminum work, there was plenty to do on the trigger mechanism. Side plates were cut from 1/8" thick stock, while the trigger itself was milled out of 1/4" material. Threaded spacers and a return spring completed the main mechanical assembly.



This drops pretty neatly into the cavity in the stock, and I cut a thin aluminum plate to cover up the mechanism.


A trigger guard was hammered over a wooden buck, then threaded for some very small machine screws and mounted to the plate.



The last part of the trigger assembly is the safe/semi/auto switch in front of the actual trigger. On a real PPSH this is a slide switch, but in the Fallout game files it's a toggle. Weird, since the gun has no full auto feature, but I just makes it like I sees it.

Moving forward and a little bit up to the barrel heat shield again, I needed to make all the bits that sit at the back near the shell eject port. The shroud around the barrel was made from ABS pipe and laminated acrylic; I cut the port on the side with the mill.

The rear sight and safety switch (I guess thats what the block behind the sight is supposed to be?) were made from acrylic parts, then molded and cast with aluminum powder in urethane resin. The stock butt plate was molded along with these parts, after being sculpted from a block of urethane tooling board.


The rear shroud slips over the barrel heat shield, and is held in place by the screws securing the iron sight and rear safety switch.

One last part was made from resin for the rear of the rifle - the barrel end cap. This was initially lathed, then put in the mill to have one side leveled off in order to lay flat over the rear stock.



You might have noticed the glossy and pretty stock in the shot above. Both the stock and the grip received several coats of wood stain, buffed with steel wool between each coat. After allowing to dry for several days, these parts were buffed with paste wax. Shiny! I also added a rear sling swivel (off a 1914 Enfield) to the rear stock.



At this point, all the major components were finished! The gun is built in such a way that it can be taken apart down to its individual components if any maintenance needs to be done (it was originally intended for a film shoot.) All parts are screwed together and there are no glue joints. Below are all the parts laid out before assembly (screws not shown) then after assembly. I did many test fits to make sure everything worked together, and there is a very specific order you have to go through to put it all into one gun.


All of the painted parts were put on hangers, then painted with black primer followed by Testor's "buffable metalizer" paint in gunmetal gray. The color on this paint is beautiful, and it can be buffed with a soft cloth to a nice metallic sheen.



Weathering was done in a fairly subtle way. The aluminum pieces were scuffed along the edges with a 220 grit sanding sponge to bring out the natural metal color underneath. Plastic and resin parts were dry brushed with enamel paint to match this effect.


After all the parts were dry brushed then clear coated and given 24 hours to dry, the gun was laid out for assembly! I'm no pro when it comes to field stripping and rebuild, so the process of making this into one finished prop took me a little under 2 hours. The finishing touch on the gun was a vintage PPSH-41 strap, shipped direct from Russia!


It's a blast to hold and you feel like a total bad ass walking around with it. I wouldn't really suggest that last part outside of your living room though, because you could easily mistake this cannon for the real thing and get in a lot of trouble!

Pics of the final shotgun, taken by my good friend Dan Almasy. Extra props in the set up really complete the look!



The butt plate on the gun is engraved with the Dracogen logo, the official sponsor of MANY things "geek" culture and the commissioner of this fine piece here.

Total time from start to finish on this project was 4 weeks. Not bad for such a complex project!

If you'd like more pics about the gun's build (believe it or not, I left a LOT out of this build description!) the please take a look at my Flickr. Larger resolution images of the finished piece can be found in my portfolio gallery.

Thanks for reading!
16 comments:
impeccable!
An impressive work of craftsmanship! Since I'm only just starting out as an Amateur prop builder, I would never expect to be able to match this kind of skill. I've seen some of your other builds, particularly the Gravity Gun, and I am quite impressed by your abilities. I've started my own blog showing my own attempts at serious prop building. If you want to see my first (and right now, only) work, here's the link. http://hyperdragonprops.blogspot.com/2012/12/crystal-crypt.html
how much would you charge for the looper blunderbus
gun? email me at dustblu5@yahoo.com
thank you
Awsome!
Now, Sword of Omens please!
It is a great !!!
Beautiful work as always.
Was this for a Fall out web series that may or may not already have a first series?
Once again. Splendid. You are a continued inspiration for prop building.
Splendid work, so much dedication in deed, congratulations ;)
Unbelievable!!! This is just a generousness showed by you. I am going to be a fan of you. :)
JUST TAKE MY MONEY !!!!
say i wanted to make a replica sword,the sword i have in mind is rather slim what materieal should i use, as I've never made anything this big and only worked with casting resisns. and casting resin from what I've heard is not very sturdy on a large scale. I've heard good things about polypropylene(as listed on various websites) but i dont know if it can be cast in a mold. If not then what mateiral should i use that is sturdy
Absolutely amazing, as per usual!
how much and how do i buy one from you!?
This was in Nuka break wasn't it...
I would like to buy any one of your fallout pieces. Please email me if you are interested at camgumby@gmail.com
I will also pay you if you make the thunder gun from call of duty black ops..or any other zombies weapon. But just so I know you saw this please email me with your response.
TAKE MY MONEY!
Would you make a 9mm pistol or a laser pistol from fallout? I am willing to pay a good amount of money. Thankyou. If your interested here's my email. evanpollington@gmail.com
Post a Comment