
I'm going to break with tradition for a sec, and show you the finished product first. This is a long, long, long post that details nearly 7 solid weeks of work, and you guys deserve to know that the long post is quite necessary, and (I think) well worth the read.
Credit goes to "scenemissingmagazine" on Flickr for this amazing photograph:

So, here's how I did it.
First thing's first, I needed blueprints. I built these in Illustrator, based off some very good reference images that the guys at 2K published in their artbooks:

Since this is such a large project, I'll break down the build process into partitions: The main body, the dome, the drill arm, the dome cage, other details, and the final paintwork.
The Main Body
Starting with the blueprints printed at full scale (HUGE) I made cross sections out of insulation foam and glued them into place. The empty areas between sections were filled with cardboard. This formed what I called the "skeleton" of the body.


The empty cavities in the skeleton were then filled in with expanding foam


After drying, the foam was carved into the shape of the main body



After this was completed (and the foam given more drying time so it would retain its shape) the entire form was covered in stretch fabric. This smoothed out a lot of the lumpiness of the foam


Accent areas around the arms, legs, and top of the body were made out of insulation foam, then glued to the body. Before coating with paint or fiberglass resin, these were covered with Ureshell to prevent the poly foam from dissolving. Certain areas on the body itself were also given a coat of Ureshell so they would not disintegrate. After this was dry, the entire body piece was given several applications of fiberglass resin.


The front flap was added using more insulation foam, and also given a coat of Ureshell and resin. After this was dry, I began hollowing out the foam and cardboard.


After adding some details on the body with foam tape, more ureshell, and more resin, I had a finished form!

The Dome
I started with a 24" smoked security camera dome off of eBay. This came from a demolished shopping center, and are actually hard to track down these days, given the much smaller size of most security cameras. I remember these all over the place as a kid.
After trimming the square edge off, I cut a disc from insulation foam to serve as the "ring" around the dome.

I made resin copies of wingnuts which were glued into place on the trim ring. About 15 of these resin duplicates weighed as much as a single wingnut. Since I had to wear this thing, every ounce saved counted!
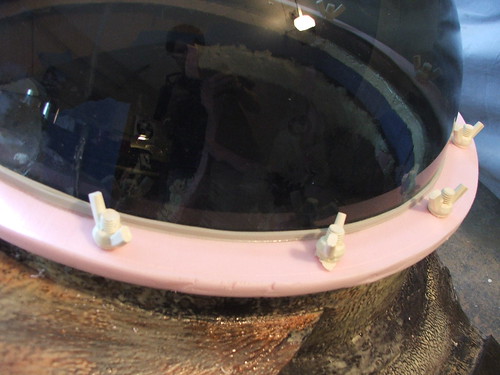
For the portholes, I made a single master out of PVC and MDF wood...

...which I molded in silicone. The portholes were all slush-cast to save weight and time in production. Also, this way, they're completely identical.

The tape here is marking the spacing of the portholes

After coating the dome in resin to thicken it a bit, I trimmed the porthole-holes with a dremel. The dome was a very brittle acrylic, so this was a nerve-wracking process!

The drill arm
Unfortunately, since this project was done in such a hurry, my process photography was somewhat lacking. The drill started out as an aluminum rod with 4 triangles of matteboard affixed to it. Rings of foam were made around the matteboard, then paper layered on top of that to create the cone shape. The actual "blade" of the drill bit is made from masking tape which has been layered in small sections to follow the curve of the drill sides.

This piece was coated in several layers of fiberglass resin (some with tinting to check coverage)

To create a really worn look, I added bits of debris to the fiberglass resin. This made a convincing textured metal finish in the end, as these parts were painted to look like rust, dents, and bits of splicer.

A PVC cage and old DeWalt 12V cordless drill make up the support frame and motor for the drill. I moved the battery inside the body of the suit to save on weight hanging from my arms.

The "housing" for this mechanism was made from a concrete tube, electrical conduit PVC and more foam tape. This was painted in ureshell to protect it during painting as well as to give it texture.

The Dome Cage
This was constructed mainly out of PVC electrical conduit. This pipe is gray in color and takes heat and bending much better than standard white PVC tubing. I bought 40 feet of it for this project and ended up using about 35. At only ¢88/10 feet though, this was an easy buy.

The sides terminate into 3" PVC couplers. These slide over 3" PVC pipe anchored to the body that has been notched to be a sightly smaller diameter than 3". Since the wearer has to enter through the front porthole, the dome as well as the cage must be removable. The front of the cage is friction-fit at the top and bottom anchorpoints, as well as the sides, so it can easily be put on and taken off.

A quick test of the body, dome, and cage. This is after the dome has had all portholes carved out and secured.

Other Details
An animatronic hand and arm extension were created for the left side of the suit. This would help prevent the "stubby arm" look I've seen on other Big Daddy suit builds


The rear tank was made from a 12" concrete tube with foam plugs on the top and bottom carved to a dome shape. The bands around the tank were made with foam tape coated in Ureshell.

I made a pushmold of some bolt heads for texture, these were cast in resin and added to the tank as well as the banding on the main body.

Boltheads and a first coat of paint on the tank. The wheel at the top is a cake decoration from our local supermarket.

The boots were made from more insulation foam. These give me about 6" of lift and make the feet look proportional to the rest of Big Daddy. I got this idea from a guy named "Duck" on the Replica Props Forum. Thanks Duck!

Painting, Weathering, and Details
Again, I apologize for my shoddy progress shots. Trying to get everything ready for Dragon*Con in time, I neglected my camera a lot.
These are the discs that go over the arms and legs. I don't have any shots handy of their creation, but they were made from layered pink foam, more Ureshell, and resin cast bolt heads. The first shot shows a raw bronze painted piece next to a completed weathered one.


The initial painting was done with hammered paint in silver and brass.

Over this went a dusting of 99¢ flat-black el-cheapo paint which was wiped off as it dried. Resin cast faux-bolts were also added to the main body as well as the drill arm before painting.



Additional weathering was done with acrylic paints, gouache, and iron powder to simulate rust. Bolt heads were touched up with silver paint so they would accent the brass better. The PET plastic in the portholes was also weathered to look grimy. After all of the above had dried, blood accents were added.



This bit of blood is my favorite part of all the weathering on the entire costume. Its details like that that I think really make the effect work.
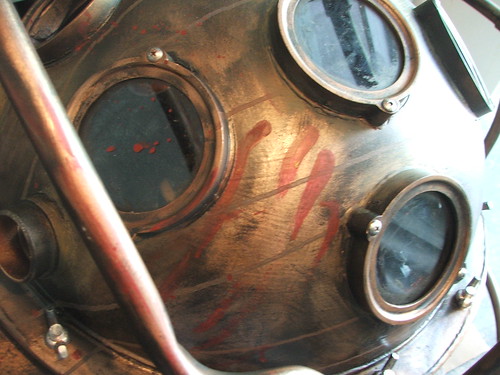
The drill was weathered in the same manner


Finally, four 3" computer case fans were added to the body and dome in order to keep the heat down. Two of these reside in the top of the suit, while the other two live in the bottom 2 ports on the dome.


Finished Result!
Since I was wearing the finished suit at Dragon*Con 2009, I don't have any pictures of my own to show! Instead, I hope the owners of these respective photographs (credited here) don't mind me showing them off a bit. My "Little Sister" is my Fiancee, Emily Keith. Our "Baby Jane Splicer" is our friend Mandie Reese.
From "mcmullets" on Flickr:

From "RJDaae" on Flickr:


From "Hueyatl" on Flickr (note, I had taken the drill arm off at this point to make walking and navigating easier)

From "Sarcasm-hime" on Flickr


A neat video of the drill working on YouTube while we were posing for the Friday Night Costume Contest photos:
And, last but totally not least, my favorite shots of all:
From "phr3qu3ncy" on Flickr:

From "scenemissingmagazine" on Flickr, a second time just because I love it so much:

This build and the execution of wearing it was more of a group effort than anything I have ever tackled before. While I did the construction of the prop myself, I did have a number of people assisting me in handling the costume during the convention itself. Emily, Mandie and I won "Best Journeyman" as well as "Best Professional Design" at Dragon*Con for this suit as well as for their costumes.
I'd like to thank my friends Ryan Shelor and Becky White for being my handlers at the convention, as well as my friend Jay (last name omitted at his request) for his build assistance during my last-minute frantic hours. I should also add that all sewing and cloth work was completed by my fiancée Emily. I cannot sew a straight line to save my life. I'd also like to thank all the random people at DragonCon (Security, Hotel Staff, etc) who assisted in helping me get around the convention while wearing this. Lastly, much thanks to the random guy who gave me a fresh, cold 12oz can of Red Stripe after our group won at the Masquerade. A celebratory beer never tasted so good.
EDIT: The suit weighs, in total, between 50 and 60 pounds. This includes all ancillary details like the drill arm, necessary batteries, shoes, etc. I was able to wear it for extended periods of time if the arms were disconnected and I was not walking. With the arms connected, I could stay in one spot for 30 minutes or so "comfortably." Walking outside in the Atlanta heat bordered on suicide.
EDIT 2: This costume is not 100% completed as of yet. I wanted to share the work after DragonCon, and I will update again when the suit is finished to my standards. Unfortunately, the clock was against me on this and some of the details suffered because of it.
I have plans to add padding to the arms and legs in order to fill them out more. Also, LEDs will be added to the front dome to simulate the red and yellow glow of the Big Daddys. The suit did suffer some minor damage at the convention (nicks and scrapes mostly. Have you ever tried getting a Big Daddy into a hotel elevator??) so there need to be some small repairs as well. For those wondering, the suit was supported by a hiking backpack mounted at 6 anchorpoints inside the main body. I felt terrible carving up a perfectly good backpack, but the end result was worth it. Further, I am a small guy! 5'7" tall and 135lb soaking wet. I'm sure someone of greater stature than I could hold out much longer under the weight of a costume like this, but muscle training just wasn't a part of the schedule. Maybe next time!
EDIT 3: The drill does spin correctly, pulling material forwards and into the bit. It looks weird in the YouTube video, but trust me on this! It also has the ability to spin much faster, albeit at the expense of my elbow joint. I tried not to spool it up to full speed too much in case something went awry (I didn't want it disintegrating into an audience or expensive camera equipment)
Emily and I are currently interested in doing a photoshoot in Atlanta with this suit and her Little Sister costume. We'd love to see about getting into the Georgia Aquarium if possible. Any chance there is someone out there that can make some calls and pull some strings?
203 comments:
«Oldest ‹Older 201 – 203 of 203 Newer› Newest»i gotta get me one of those
Hey Volpin!
You inspired us! Using your guide (with a few of our own adjustments) we created our own Big Daddy suit for the 2013 Salt Lake Comic con and got first place!! Thank you for paving the way!
http://bigdaddycosplay.blogspot.com/2013/09/big-daddy-september-2013.html
Michelle
WOW THAT IS GREAT!!!! I want to try to make the delta big daddy but i cant find the pep, files anywhere...
Post a Comment